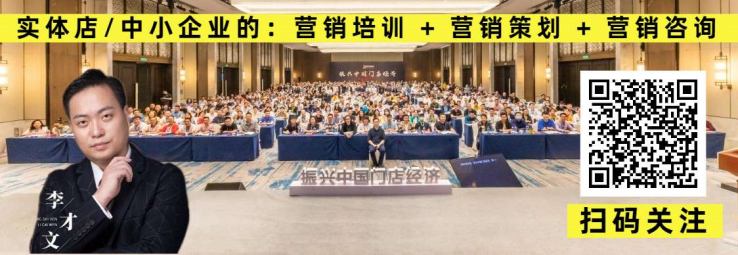
品茗论道话质量,共探管理六大利器。在当今激烈的市场竞争中,汽车行业及其他制造业对于产品质量的要求愈发严格。为了确保产品从设计到生产都能满足客户的高标准,六大核心工具应运而生。今天,我们将深入探讨这六大工具的精髓,期待与粉丝们共同讨论,碰撞出更多的质量管理的火花。
一、产品先期质量策划(apqp)
apqp是一种系统化的方法,旨在确保新产品从设计到生产各阶段均能满足客户要求。它跨越多个部门,涉及设计、工程、生产、采购、质量控制等环节。通过apqp,我们能够提前识别潜在问题,减少后期返工和改进成本,从而提升整体的产品质量。
二、生产件批准程序(ppap)
ppap是供应商向客户提交的一系列文件和样品,用以证明其生产的产品符合客户要求,并获得批量生产的批准。这包括设计记录、过程流程图、控制计划等文件,以及实际的样品。通过ppap,客户可以评估供应商的生产能力,确保产品的质量。
三、故障模式与影响分析(fmea)
fmea是一种前瞻性的分析工具,用于识别产品或过程中可能出现的故障模式及其潜在影响。通过评估严重性、发生概率和检测难度,我们可以确定风险优先数,并采取相应的预防措施,从而降低产品失效的风险,提高产品的可靠性和稳定性。
四、统计过程控制(spc)
spc是一种使用统计方法监控过程变异的工具。它通过收集和分析生产过程中的数据,识别和纠正生产过程中的变异,从而确保产品的质量稳定和一致性。spc能够帮助我们及时发现异常情况,防止不合格品的产生。
五、测量系统分析(msa)
六、控制计划(cp)
cp是一个动态文件,描述了在生产过程中需要监控的特性、测量方法、频率和控制手段。它包括对生产过程中的关键参数和控制点的定义和监控,旨在确保产品的质量符合要求。通过cp,我们可以及时发现和纠正生产过程中的问题,防止不合格品的产生。
这六大工具共同构成了汽车行业及其他制造业质量管理体系的核心。它们分别从产品设计、生产件批准、故障预防、过程监控、测量系统以及生产控制等多个方面,为企业的质量管理提供了全面的支持。通过灵活运用这些工具,企业可以更好地满足客户需求,提高市场竞争力。希望广大读者能够通过深入理解这些工具的精髓,将其运用于实际工作中,为企业的发展贡献力量。
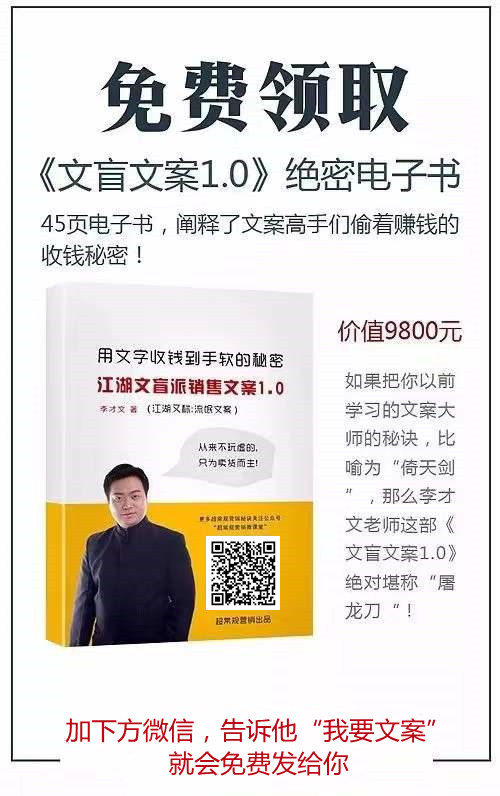